การคำนวนหา Load ของระบบ
ก่อนที่จะเลือกอุปกรณ์ที่ใช้สำหรับถังจำเป็นต้องคำนวณค่าพลังงานความร้อนที่ต้องการเพื่อนำค่าดังไปใช้ในการเลือกขนาดของอุปกรณ์ไอน้ำในระบบทำความร้อน โดยการคำนวณจะแบ่งระบบเป็นสองช่วงได้แก่
· ช่วงอุ่นระบบก่อนใช้งาน Cold start-up conditions.
· ช่วงระบบใช้งาน Normal running conditions.
โดนก่อนที่จะคำนวณพลังงานที่จะใช้ในสองสถานการณ์ด้านบนจำเป็นต้องรู้ค่าดังนี้
· อุณหภูมิที่เพิ่มขึ้นของผิวถังจนถึงอุณหภูมิใช้งาน Raising the Tank Structure Temperature
· อุณหภูมิที่เพิ่มขึ้นของของเหลวจนถึงอุณหภูมิใช้งาน Raising the Liquid Temperature
· ค่าความร้อนสูญเสียที่ผิวถังขณะอุ่นระบบและทำงาน Heat Losses from Tank Surfaces
· ค่าความร้อนสูญเสียที่ผิวของเหลวขณะอุ่นระบบและทำงาน Heat Losses from Liquid Surface
· ค่าความร้อนที่ต้องการให้กับผลิตภัณฑ์ขณะทำงาน Heat Absorbed by Material being Processed
· ปริมาณน้ำร้อนที่หายไปซึ่งจะเท่ากับปริมาณน้ำเย็นที่ต้องเติมในระบบ
สำหรับเวลาที่ใช้ในช่วงอุ่นเครื่องให้ได้อุณหภูมิที่ต้องการ ส่วนใหญ่เราต้องการอุ่นเครื่องให้เร็วที่สุด โดยการออกแบบอาจทำให้ลืมผลกระทบที่เกิดขึ้นกับ boiler และ steam system หรืออาจลืมคิดถึงภาวะอากาศเช่นในช่วงหน้าหนาวที่อาจส่งผลกระทบต่อระบบได้
Raising the Tank Structure Temperature
Heat Required = Weight Of Metal x Specific Heat x Temperature Rise.
Raising the Liquid Temperature
Heat Required = Weight Of Liquid x Specific Heat x Temperature Rise.
สำหรับค่า Specific Gravity and the Specific Heat ของของเหลวอาจใช้น้ำแทนได้แต่ค่าที่ได้อาจไม่ถูกต้อง
Heat Losses from Tank Surfaces
ในกรณีที่อากาศรอบถังมีความเร็วให้คูณค่าปรับแก้โดยสามารถดูได้จากตารางด้านล่าง กรณีที่ถังมีการหุ้มฉนวนความเร็วของอากาศรอบถังมีผลน้อยมาก ที่ความเร็วลมประมาณ 5 m/s จะมีลักษณะลมพัดเบา ๆ ถ้าลมที่ความเร็ว 10 m/s จะมีลมพัดเย็นสบาย ถ้าความเร็ว 16 m/s ลมจะมีลักษณะพัดแรง
การประมาณค่าพลังงานความร้อนสูญเสียระหว่างผิวของเหลวไม่ได้ขึ้นอยู่กับอุณหภูมิที่แตกต่างอย่างเดียวแต่ยังมีอีกหลายปัจจัยได้แก่
· อุณหภูมิของของเหลว โดยเฉพาะอุณหภูมิที่ใกล้จุดเดือด
· ความเร็วของอากาศที่สัมผัสกับผิวของเหลว
· ความปั่นป่วนผิวของของเหลว
· ส่วนปัจจัยที่ส่งผลกระทบไม่มากได้แก่ ความชื้นและอุณหภูมิของอากาศ
สภาวะในช่วงอุ่นเครื่อง และ ช่วงทำงาน ต้องให้ความใส่ใจเป็นพิเศษเพราะการสูญเสียความร้อนที่ผิวของเหลวไม่เป็นสัดส่วนเท่ากัน (Non linear) โดยในแต่ละช่วงสามารถหาได้ดังนี้
Running Load ในช่วงทำงานสามารถหาการสูญเสียได้จากกราฟด้านล่าง เมื่อทราบอุณหภูมิของของเหลวให้ลากเส้นลงในแนวตั้งจนเจอเส้นหนาหลังจากนั้นให้ลากเส้นในแนวนอนไปที่แกน Y จะได้ค่าการสูญเสียพลังงานความร้อน
Warm up Load สำหรับการสูญเสียพลังงานความร้อนที่ผิวของเหลวในช่วงอุ่นเครื่องอุณหภูมิแตกต่างระหว่างของเหลวกับอากาศจะเริ่มจากศูนย์ดังนั้นจากกราฟด้านบนค่าที่ได้จะต้องหารสองเพื่อเป็นค่าเฉลี่ย
ค่าในกราฟด้านบนคิดอุณหภูมิอากาศที่ 15.6°C และความชื้นที่ 55%
สำหรับในกรณีที่อากาศมีการเคลื่อนที่บนผิวของเหลวเช่นเกิดจากการเปิดประตูห้องค้างไว้หรือการวางถังในที่โล่ง ค่าพลังงานความร้อนที่สูญเสียจะมีค่ามากขึ้นโดยสามารถหาได้จากกราฟด้านบนโดยลากค่าความร้อนสูญเสียในกรณีอากาศนิ่งมาตัดกับเส้นความเร็วอากาศ จากจุดตัดให้ลากเส้นลงในแนวดิ่งจะได้ค่าความร้อนสูญเสียกรณีอากาศมีความเร็ว
สำหรับถังบางประเภทเช่นถังเคมีจะมีการดูดควันที่เกิดขั้นเพื่อระบายออกด้านอกทำให้อากาศที่ผิวของเหลวมีความเร็วมากขึ้น โดยความเร็วเราสามารถคำนวณได้จากระยะระหว่างช่องว่างหัวดูดกับของเหลว
Inlet area = 4 x 1.25 x 0.05 = 0.25 m2
Fan rating = 1 m3/s
Total volume = inlet area x velocity
1 = 0.25 x velocity
อีกหนึ่งวิธีที่ช่วยในการลดการถ่ายเทความร้อนระหว่างผิวของเหลวกับอากาศคือการใส่ลูกบอลพลาสติก โดยปกติลูกบอลจะมีขนาดประมาณ 50 mm ซึ่งทำจากวัสดุ polypropylene จึงสามารถใช้กับสารเคมีที่มีการกัดกร่อนได้ โดยบอลดังกล่าวจะลอยอยู่บนผิวหน้าของเหลว ซึ่งวิธีนี้สามารถลดการสูญเสียพลังงานได้มากถึง 70% และลดการละเหยกลายเป็นไอได้ถึง 90% สำหรับวิธีนี้อาจต้องระวังในกรณีที่บอลอาจเข้าไปอุดตันในท่อน้ำเข้าออกได้
Heat Absorbed by Material being Processed
Heat absorbed = Weight Of Material x Specific Heat x Temperature Rise.
ตัวอย่าง
การคำนวณหาพลังงานที่ต้องการ โดยถังบรรจุน้ำที่อุณหภูมิเริ่มต้น 15 oC และให้ความร้อนจนถึง 70 oC ภายใน 3 ชั่วโมง เมื่อถึงอุณหภูมิใช้งานชิ้นงานเหล็กขนาด 500 kg (Specific Heat 0.67 kJ/kg.K) ที่อุณหภูมิ 15 oC จะถูกใส่ลงในถังทุก ๆ 15 นาที สมมุติให้อากาศโดยรอบอุณหภูมิเท่ากับ 15 oC.
ช่วงอุ่นเครือง Warm Up Load
Total heat required = Heat to raise the water temp. + Heat loss from tank surfaces
+ Heat loss from liquid surface
- Heat to raise the water temp. = Mass of Water x Specific Heat x Temperature Rise
= (1.5 x 1.5 x 3.0 x 1000) x 4.186 X 55 = 1 554 053 kJ
แต่ระบบต้องการให้ร้อนภายใน 3 ชั่วโมง ดังนั้นจะต้องใช้พลังงานความร้อนเท่ากับ:
1554053/(3 x 3600) = 144 KJ/s = 144 KW
- Heat loss tank surfaces = Heat loss (Table) x Surface area x diff. Average Temp
ความร้อนที่ผิวถังเพิ่มขึ้นจาก 15 เป็น 70 องศาดังนั้นค่าเฉลี่ยเท่ากับ (70-15)/2 = 27.5 องศา
= 10.6 X (2(3 x 1.5) + 2(1.5 x 1.5)) x (70-15)/2 = 3.94 kW
- Heat loss from the water = Average Heat loss (Fig. 1) x Surface area of the water
= (5500/2) x (1.5 x 3.0) = 12.37 kW
Total Warm Up Heat Load = 144 kW + 3.94 kW + 12.4 kW = 160 kW
ช่วงใช้งาน Running Load
Total heat required = Heat absorbed by steel + Heat loss from tank surfaces
+ Heat loss from liquid surface
- Heat absorbed by the steel = Mass of steel x Specific Heat x Temperature Rise
= 500 x 0.67 x (70 - 15) = 18 425 kJ
แต่ระบบมีการเติมเหล็ก 500 kg ทุก ๆ 15 นาที ดังนั้นจะต้องใช้พลังงานความร้อนเท่ากับ
(18425 x 4 ครั้งต่อชั่วโมง)/3600 = 20.5 KJ/s = 20.5 KW
- Heat Loss Tank Surfaces = Diff. Temp. Tank & Air x Heat loss (table 1) X Surface area
= (70 - 15) x 11.7 x (2(3x1.5)+2(1.5x1.5)) = 8.7 kW
- Heat Loss from Liquid Surface = Heat loss (Flg1)x Surface area of the Liquid m2
= 5,500 x (1.5 x 3) = 24.8 kW
Total Running Load = 20.5 kW + 8.7 kW + 24.8 kW = 54 kW
สรุป
จากข้อมูลด้านบนเราสามารถเลือกอุปกรณ์ควบคุมในระบบได้ จากตัวอย่างเราจะใช้โหลดที่สูงสุดคือช่วงอุ่นเครื่องเท่ากับ 160 kW
Tank heating by direct steam injection
ข้อดีสำหรับการทำความร้อนโดยตรงหรือการฉีดไอน้ำผสมกับน้ำโดยตรง
- เป็นการทำความร้อนที่งายและประหยัดที่สุดเนื่องจากไม่จำเป็นต้องมีอุปกรณ์แลกเปลี่ยนความร้อน สตีมแทร็ป ไม่ต้องเดินท่อน้ำคอนเดนเสท
- สำหรับบางกระบวนการที่ต้องการให้ของเหลวที่จะให้ความร้อนเกิดการปั่นป่วนเช่นการผสม วิธีนี้ก็จะช่วยให้กระบวนการสมบูรณ์มากยิ่งขึ้น
- สำหรับวิธีการฉีดไอน้ำโดยตรงกระบวนการจะต้องสามารถยอมรับการเจือจางได้เนื่องจากน้ำที่กลั่นตัวจากไอน้ำจะเข้าไปผสมกับของเหลวในกระบวนการ
- ความร้อนจากไอน้ำสามารถให้พลังงานกับกระบวนการได้มากกว่าเนื่องจากพลังงานที่อยู่ในน้ำคอนเดนเสทก็สามารถนำมาใช้ได้ทั้งหมด
ตัวอย่าง
จากตัวอย่างด้านบนถ้าระบบทำความร้อนโดยการฉีดไอน้ำโดยตรงที่แรงดัน 2 bar g ในน้ำอุณหภูมิ 70 oC
Enthalpy of evaporation for steam at 2 bar g = 2136.3 kJ/kg
Saturation temperature of steam at 2 bar g = 134 oC
เมื่อน้ำร้อน 134 oC ถูกผสมลงในน้ำ 70 oC น้ำร้อนจะลดอุณหภูมิลงเหลือ 70 oC ทำให้เกิดพลังงานส่วนเกินขึ้น
(134 - 70) x 4.186 kJ/kg oC = 269.7 kJ/kg
นั้นหมายความว่าเราสามารถใช้พลังงานไอน้ำได้มากถึง 2136.6 + 269.7 = 2404.2 kJ/kg
ดังนั้นจากตัวอย่างถังเก็บน้ำด้านบนที่กระบวนการต้องการพลังงาน 160 kW สำหรับการให้ความร้อนจากไอน้ำโดยตรงจะต้องใช้ไอน้ำเท่ากับ
160 / 2404.2 x 3600 = 240 kg/h
Steam Injection at Low Pressure
การฉีดไอน้ำโดยตรง ไอน้ำจะถูกฉีดในน้ำโดยไอน้ำฟองเล็ก ๆ จะลอยขึ้นด้านบน สำหรับกระบวนการที่ดีฟองไอน้ำจะต้องควบแน่นกลายเป็นน้ำและฟองจะต้องหายไปก่อนที่จะถึงผิวน้ำ ในบางกรณีอาจติดตั้งแผ่นประทะเพื่อป้องกันฟองไอน้ำลอยถึงผิวน้ำก็ได้
ขนาดของฟองไอน้ำ
ในการฉีดไอน้ำให้แลกเปลี่ยนความร้อนกับน้ำสิ่งสำคัญก็คือพื้นที่แลกเปลี่ยนความร้อนซึ่งก็คือปริมาณพื้นที่ผิวของฟองไอน้ำนั้นเอง อย่างไรก็ตามการแลกเปลี่ยนความร้อนต้องทำให้เสร็จก่อนที่ฟองไอน้ำจะลอยขึ้นสู่ผิวน้ำเพราะจำทำให้ความร้อนหายไปกับอากาศ ดังนั้นจึงต้องทำให้ไอน้ำมีขนาดเล็กเนื่องจากพลังงานน้อยพื้นที่ผิวมากสามารถแลกเปลี่ยนความร้อนได้เร็ว
ถ้าใช้ท่อปลายเปิดฟองไอน้ำที่ได้จะมีขนาดใหญ่ ดังนั้นโดยปกติจะใช้ท่อปลายปิดแต่เจาะรูเล็ก ๆ ตลอดความยาวท่อ ยิงรูเล็กขนาดของไอน้ำก็จะเล็กตามไปด้วย โดยปกติขนาดประมาณ 2 ถึง 5 mm นอกจากนี้ขนาดของฟองไอน้ำยังถูกกำหนดด้วยแรงดันไอ ซึ่งถ้าแรงดันมากความหนาแน่นของไอน้ำจะมีมากดังนั้น พื้นที่ผิวต่อมวลไอน้ำจะลดลง โดยปกติแรงดันไอน้ำมักจะไม่เกิน 2 bar g
ความเร็วของฟองไอน้ำ
ความเร็วของฟองไอน้ำจะขึ้นอยู่กับผลต่างแรงดันไอน้ำกับแรงดันน้ำ ณ หัวฉีดซึ่งคิดจากความสูงของน้ำจากหัวฉีดถึงผิวน้ำ ซึ่งเมื่อฟองไอน้ำเคลื่อนที่ผ่านของเหลวของเหลวจะเข้ามาแทนที่เมื่อฟองไอน้ำเคลื่อนที่ผ่านทำให้เกิดเสียงขึ้นซึ่งจะทำให้เกิดอาการสั่นตามมา ดังนั้นอาการสั่นจะขึ้นกับแรงดันไอและขนาดของรูเจาะโดยตรง
ขนาดท่อสำหรับพ่นไอน้ำ
สำหรับไอน้ำที่ใช้ปกติจะมีความเร็วที่ 25 m/s ขึ้นไปแต่สำหรับหัวฉีดจะลดความเร็วให้เหลือเพียง 15 m/s
Table 2 Pipeline Capacities (kg/hr) at Specific Velocities
ขนาดรูเจาะสำหรับพ่นไอน้ำ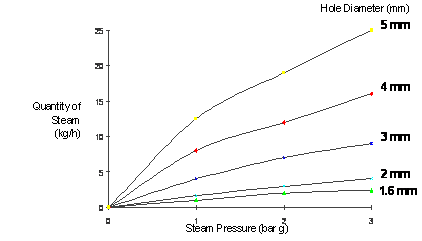
Fig. 2 Sparge Hole Size
อัตราการไหลของไอน้ำผ่านรูเจาะที่ขนาดและแรงดันต่าง ๆ ได้แสดงในภาพที่ 2 ซึ่งจะเห็นได้ว่าแรงดันที่ใช้ไม่ควรต่ำกว่า 2 bar g
ตำแหน่งรูเจาะ
ถ้าเจาะรูด้านบนของท่อไอน้ำจะพุ่งขึ้นด้านบนอย่างรวดเร็วทำให้เกิดเสียงดัง ดังนั้นการเจาะรูจะเจาะด้านล่างของท่อซึ่งเมื่อไอน้ำพุ่งออกลงด้านล่างจะทำให้สามารถเพิ่มเวลาในการแลกเปลี่ยนความร้อนด้วย แต่ถ้าไอน้ำพุ่งลงกระแทกกับพื้นถังอย่างเร็วอาจทำให้เกิดการกัดเซาะบริเวณพื้นถังได้ดังนั้นจึงต้องเว้นระยะห่างประมาณ 0.3 m
Example ตัวอย่างการหาขนาดรูเจาะ
จากตัวอย่างด้านบนเราต้องการพลังงานความร้อนเท่ากับ 160 kW ที่แรงดันไอน้ำ 2 bar และอัตราการไหลเท่ากับ 240 kg/h
การหาขนาดท่อและรูเจาะ
จากตารางที่ 2 ท่อขนาด 2 นิ้วที่ความเร็ว 25 m/s อัตราการไหลอยู่ที่ 323 kg/h ดังนั้นถ้าอัตราการไหลที่ 240 kg/h ความเร็วไอน้ำจะลดลงอีก
จากรูปที่ 2 ที่แรงดันไอน้ำ 2 bar g รูเจาะขนาด 3 mm อัตราการไหลอยู่ประมาณ 7 kg/h ดังนั้นจะต้องเจาะทั้งหมด 240/7 = 35 รู
การเจาะรูจะต้องเจาะขนาดเท่ากันและตำแหน่งด้านล่างของกึ่งกลางท่อ โดยสามารถเจาะด้านเดียวหรือสองด้านก็ได้
สำหรับหัวฉีดแรงดันสูงจะทำให้เกิดการปั่นป่วนในบริเวณที่ไอน้ำและน้ำผสมเข้าด้วยกัน ถ้าการผสมเป็นไปอย่างถูกต้องฟองไอน้ำจะไม่ลอยจนถึงผิวของของเหลว สำหรับกระบวนการนี้จำเป็นที่ต้องใช้เครื่องมือที่มีคุณภาพมากเพื่อให้การทำงานมีประสิทธิภาพ
Methods of High Pressure Steam Injection - Silent Water Heater
เครื่องมือดังกล่าวสามารถติดด้านนอกหรือด้านในถังก็ได้ การทำงานงายไม่ต้องใช้ปั๊มไม่มีชิ้นส่วนเคลื่อนที่ ไอน้ำและน้ำจะผสมกันกลายเป็นน้ำร้อน การควบคุมความร้อนจะอาศัยวาล์วควบคุมการเปิด ปิดไอน้ำอีกครั้ง สำหรับอุปกรณ์ดังกล่าวจะต้องควบคุมแรงดันให้คงที่ ถ้าแรงดันมากเกินจะทำให้ความเร็วไอและอัตราการไหลเพิ่มขึ้นซึ่งเป็นสาเหตุทำให้เกิดเสียงดังและการสัน อัตราการไหลสูงสุดอยู่ที่ 50 kg/h ถ้าต้องการอัตราการไหลที่เพิ่มขึ้นจะต้องติดอุปกรณ์ดังกล่าวเพิ่มโดยการต่อแบบขนาน
ตัวอย่าง
จากตัวอย่างด้านบนถ้าระบบต้องการพลังงานจำนวน 160 kW โดยใช้ไอน้ำขนาด 7 bar g จะต้องใช้ไอน้ำปริมาณ 233 kg/h
Fig. Sizing Chart for Silent Water Heater
การหาจำนวนหัวฉีด
จากกราฟด้านบนที่แรงดันไอน้ำ 7 bar g อัตราการไหลไอน้ำเท่ากับ 34 kg/h ดังนั้นจะต้องติดตั้งอุปกรณ์ดังกล่าวจำนวน 7 ตัว ซึ่งจำนวนดังกล่าวเป็นจำนวนที่ไม่ทำให้เกิดปัญหาของเสียงดังแต่ถ้าระบบไม่เน้นปัญหาเรื่องเสียงอาจลดจำนวนลงได้ ซึ่งจะเห็นได้ว่าหลังจากผ่านช่วงอุ่นเครื่องปริมาณการใช้ไอน้ำจะลดลง
การติดตั้ง
Methods of Steam Injection at High Pressure - Injector
การทำงานของอุปกรณ์ดังกล่าวน้ำเย็นจะเคลื่อนที่เข้าสู่อุปกรณ์บริเวณรูที่อยู่ด้านข้างและจะผสมกับไอน้ำกลายเป็นน้ำร้อนพ่นออกมาทางด้านหน้า การติดตั้งหัวฉีดจะต้องติดตั้งภายในถัง โดยที่ตำแหน่งการติดตั้งมีผลต่อการผสมระหว่างน้ำและไอน้ำ สำหรับปัญหาด้านเสียงอาจเกิดได้ถ้าแรงดันไอน้ำมีมากขึ้น
1. Normal Running
การทำงานปกติจะเกิดเสียงน้อย แรงดันไออยู่ระหว่าง 2 bar g ความร้อนของน้ำหลังออกจากหัวฉีดจะเพิ่มขึ้นประมาณ 10°C แรงดันในช่วงนี้สามารถเพิ่มขึ้นได้มากถึง 8 bar g โดยช่วงแรงดันดังกล่าวอาจมีเสียงดังและสันสะเทือนเกิดขึ้นได้แต่ไม่มาก
2. Incomplete Condensation
ช่วงนี้จะเกิดแรงสั้นสะเทือนและเสียงดังมากเนื่องจากน้ำมีอุณหภูมิสูงเกิน 90°C การถ่ายเทความร้อนจากฟองไอน้ำทำได้น้อยลงทำให้มีไอน้ำบางส่วนลอยผ่านถึงผิวน้ำซึ่งจะมีลักษณะคลายน้ำเดือด ไม่แนะนำให้ใช้ถังแบบเปิดโล่งเนื่องจากโครงสร้างไม่แข็งแรงเท่ากับถังรับแรงดัน
3. Low Flow rates
เมื่อแรงดันในหัวฉีดลดลงน้อยกว่า 1.5 bar g จะเกิดเสียงดังที่หัวฉีด เนื่องจากที่แรงดันดังกล่าวไอน้ำไม่พ่นออกมาได้ทำให้เกิดการเดือดขึ้นที่บริเวณหัวฉีด และระบบท่อ ซึ่งปัญหาดังกล่าวอาจเกิดจากการเลือกขนาดหัวฉีดที่ใหญ่เกินก็ได้
ตัวอย่าง
จงหาขนาดหัวฉีดสำหรับทำความร้อนที่ 160 kW โดยใช้ไอน้ำแรงดัน 7 bar g ที่อัตราการไหล 233kg/h
การหาขนาด
จากรายละเอียดหัวฉีดในรูปด้านบน เราสามารถเลือกขนาดได้เป็น IN25 ซึ่งสามารถให้ไอน้ำผ่านได้มากถึง 560 kg/h ถ้าไอน้ำไม่เพียงพออาจติดตั้งมากกว่าหนึ่งหัวฉีดก็ได้
การติดตั้ง
Tank heating by Coil
การทำความร้อนด้วยวิธีนี้จะมีคอยล์ร้อนทำหน้าที่แลกเปลี่ยนความร้อน โดยที่น้ำคอนเดนเสทจะถูกระบายออกจากแทร็ปทังหมด
Loop Seal ที่ตำแหน่งล่างสุดของคอยล์ร้อนดังรูปด้านล่างซึ่งจะต่อเข้ากับท่อขนาดเล็กกว่าเพื่อทำหน้าที่ส่งน้ำคอนเดนเสทออกจากระบบผ่านแทร็ป ถ้าไม่มี loop seal ไอน้ำจะสามารถวิ่งผ่านไปยังสตีมแทร็ป ทำให้น้ำคอนเดนเสทที่เกิดขึ้นใหม่ไม่สามารถไหลเข้าไปแทนที่ไอน้ำจนกว่าไอน้ำที่ค้างอยู่ในท่อจะกลั่นตัวกลายเป็นน้ำเสียก่อน ได้ปัญหานี้เรียกว่า 'Steam Locking' ปัญหานี้จะทำให้เกิดน้ำท่วมขังภายในคอยล์
สาเหตุที่ท่อต่อหลังจาก loop seal จะต้องมีขนาดเล็กไม่ใช้แค่ต้องการลดปริมาตรของไอน้ำที่อาจไหลผ่านไป แต่ยังช่วยป้องการเกิดฟองของไอน้ำในท่อด้วยทำให้น้ำไหลผ่านได้ง่ายขึ้น ในกรณีที่ไม่สามารถลดขนาดท่อได้เนื่องจากปัญหาการกัดกร่อนบริเวณรอยต่ออาจใช้ท่อขนาดเล็กประมาณ 6 ถึง 10 mm สวมลงตรงกลางและซีลเหนือของเหลวดังรูปก็ได้
การติดตั้งคอยล์
มีทั้งหมดสามแบบได้แก่
Bottom Coils
เป็นการติดตั้งคอยล์อย่างง่าย โดยการติดตั้งที่ส่วนล่างของถัง ไอน้ำเข้าและน้ำออกผ่านผนังถังด้านข้าง ในกรณีที่ของเหลวภายในถังมีการกัดกร่อนวัสดุอาจใช้เป็นสแตนเลสและยกท่อด้านเข้าและออกเหนือขอบถังก็ได้
เป็นการติดตั้งคอยล์มากกว่า หนึ่งชุดเพื่อให้ความร้อนภายในถังอย่างสม่ำเสมอโดยมีอุปกรณ์ควบคุมแยกออกจากกันอย่างอิสระ
Side Hung Coils
เป็นการติดตั้งคอยล์ร้อนแบบไม่ถาวรใช้ในกรณีที่ของเหลวมีผลกัดกร่อนต่อวัสดุที่ใช้ผลิตคอยล์แน่นอนหากมีการแช่ทิ้งไว้นาน ๆ หรือระบบที่ต้องการหยุดการให้ความร้อนแบบทันทีทันไดโดยการยกคอยล์ร้อนออกจากถัง คอยล์จะมีลักษณะคล้ายงูดังรูปด้านบน น้ำคอนเดนเสทจะไหลลงมาอยู่ด้านล่างและผ่าน Loop seal ก่อนที่จะไหลผ่านท่อขนาดเล็กเข้าสู่แทร็ป
การควบคุมอุณหภูมิภายในถัง
การติดตั้งคอยล์ร้อนจะต้องให้ความสนใจการกระจายความร้อนตลอดแนวของถัง ซึ่งขึ้นอยู่กับขนาดของคอยล์และความยาว สำหรับถังที่มีขนาดยาวมาก ๆ และใช้อุปกรณ์ชุดเดียวท่อจะต้องลาดเอียงตลอดแนวยาวถัง ซึ่งอาจเกิดปัญหาความร้อนไม่เท่ากันตลอดถังถ้าติดตั้งวาล์วควบคุมใกล้กับช่องทางไอน้ำเข้า ที่บริเวณใกล้กับทางออกแรงดันจะลดลงเนื่องจากการเกิดการควบแน่นของไอน้ำทำให้ประสิทธิภาพในการแลกเปลี่ยนความร้อนลดลงด้วยอาจเหลือเพียง 40 % นอกจากนี้บางกรณีที่ปลายท่ออาจเกิดเป็นสุญญากาศซึ่งจะก่อให้เกิดปัญหา Water logging ทำให้อุณหภูมิของเหลวภายในถังลดลงหลังจากวาล์วควบคุมเปิดไอน้ำที่เข้าสู่คอยล์จะเป็นสาเหตุทำให้เกิด water hammer ตามมา
ประสิทธิภาพการถ่ายเทความร้อนของคอยล์ให้กับของเหลวภายในถังสามารถคำนวณได้จากสมการ
Q = UA(T diff)
โดย
Q = The rate of heat transfer (kW)
U = The heat transfer coefficient (kW/m2 ºC)
A = The heat transfer area (m2)
T diff= The temperature difference between the heating medium and the liquid in the tank.
การออกแบบอุปกรณ์แลกเปลี่ยนความร้อนจะดูที่ค่า U x A ซึ่งเป็นค่าคงที่ขึ้นอยู่กับประสิทธิภาพของอุปกรณ์ ดังนั้นถ้าจะเพิ่มพลังงานความร้อน (Q) จะต้องเพิ่มความแตกต่างของอุณหภูมิระหว่างคอยล์กับของเหลว (T diff) ซึ่งก็คือการควบคุมอุณหภูมิของไอน้ำนั้นเอง
สำหรับค่า U จะถูกออกแบบมาจากผู้ผลิตซึ่งอาจแตกต่างจากค่าในตารางขึ้นอยู่กับวัสดุที่นำมาใช้ผลิตคอยล์ สำหรับการทำความร้อนในพื่นที่เล็ก ๆ ของเหลวอยู่รอบ ๆ คอยล์ให้พิจารณาจากอุณหภูมิของน้ำและไอน้ำเป็นหลัก ถ้าเกิดเป็นถังที่มีขนาดใหญ่ให้พิจารณาจากแรงดันและระบบหมุนเวียนของน้ำในถังซึ่งถ้าถังมีระบบหมุนเวียนของน้ำที่ดีจะช่วยให้การถ่ายเทความร้อนได้มากขึ้น ในกรณีที่ของเหลวไม่ใช้น้ำค่าที่ได้จะแตกต่างจากในตาราง
ตัวอย่าง
กำหนดให้ระบบต้องการพลังงาน 160 kW และอุณหภูมิของเหลวเท่ากับ 70 oC ไอน้ำสำหรับคอยล์ร้อนแรงดัน 3 bar g จงหาความยาวของคอยล์
จากสมการ Q = UA(T diff)
จากตารางไอน้ำที่แรงดัน 3 bar g อุณหภูมิเท่ากับ 144 oC
T diff = 144 - 70 = 74 oC
จากตารางค่า U ที่ผลต่างอุณหภูมิ 74 oC ค่าประมาณ 1.5 kW/m2 oC
ดังนั้น 160 kW = 1.5 kW/m2 oC x A x 74 oC
A = 1.44 m2
จากตารางไอน้ำค่า Enthalpy of evaporation (hfg) สำหรับไอน้ำที่แรงดัน 3 bar g = 2134 kJ/kg
ดังนั้นระบบต้องการไอน้ำ
จากตารางความเร็วของไอน้ำในท่อที่ความเร็ว 25 m/s ท่อขนาด 40 mm สามารถให้ไอน้ำไหลผ่านเท่ากับ 256 kg/h ใกล้เคียงที่ต้องการดังนั้นจึ่งเลือกขนาดท่อ 40 mm
จากตารางท่อขนาด 40 mm มีพื้นที่แลกเปลี่ยนความร้อน 0.15 ตารางเมตร/ความยาวท่อ1เมตร ดังนั้นต้องใช้ท่อยาว
Area = Area Pipe x Length
Length = 1.44/0.15 = 9.6 เมตร
ในการทำงานจริงท่อขนาดเล็กจะสามารถบิดงอได้มากกว่า ดังนั้นจึ่งมีการเลือกใช้ขนาดของคอยล์ที่เล็กลงโดยอาจต่อขนานกันเพื่อให้ความเร็วของไอน้ำภายในคอยล์ไม่มากจนเกินไปดังรูปด้านล่าง ซึ่งในกรณีที่ความเร็วของไอน้ำในคอยล์เพิ่มขึ้น อาจต้องพิจารณาการติดตั้งและออกแบบเพื่อหลีกเลี่ยง Water hammer โดยการหาวิธีระบายน้ำคอนเดนเสทออก
ค่าที่ได้จากการคำนวนเมื่อนำไปติดตั้งอาจไม่สามารถให้ความร้อนกับระบบได้อย่างสม่ำเสมอ ถ้าคอยล์ใหม่สะอาดปราศจากคราบหินปูนหรือตะกรันการแลกเปลี่ยนความร้อนอาจทำได้ดี แต่ถ้ามีการใช้งานไปนาน ๆ เมื่อมีคราบต่าง ๆ มาเกาะจะทำให้การแลกเปลี่ยนความร้อนลดลงดันนั้นในการออกแบบจะต้องเพิ่มพื้นที่แลกเปลี่ยนความร้อนให้มากขึ้น จึงเป็นไปไม่ได้ที่จะนำค่าที่คำนวณได้มาผลิตคอยล์จริง ๆ ซึ่งอาจต้องมีค่าเผื่อถึง 20%
การเลือกสตีมแทร็ป
หลังจากการเลือกขนาดคอยล์อุปกรณ์ตัวต่อไปที่จำเป็นก็คือแทร็ป การเลือกแทร็ปที่ดีจะทำให้ระบบทำงานได้อย่างมีประสิทธิภาพ สำหรับกระบวนการที่คอนเดนเสทมีการยกขึ้นผ่าน loop จะต้องใช้ท่อขนาดเล็ก แทร็ปที่ใช้ได้จะมี TD, TS, Float Thermostatic สำหรับบางกระบวนการที่คอยล์มีการรั่วซึมอาจมีสารเคมีหลุดติดมากับน้ำซึ่งก่อให้เกิดการกัดกร่อนต่ออุปกรณ์ แนะนำให้ใช้ TD ถ้าคอยล์ต่อออกด้านข้างของถังแทร็ปที่สามารถใช้ได้ประกอบด้วย TD, TS, Float Thermostatic
การควบคุมอุณหภูมิ
ปัจจัยสำคัญที่ต้องพิจารณาในการควบคุมอุณหภูมิของระบบทำความร้อน
1.บางระบบต้องการความเที่ยงตรงในการควบคุมซึ้งถ้าอุณหภูมิมากหรือน้อยเกินไปอาจทำให้ผลิตภัณฑ์เสียหายได้
2. การทำงานของวาล์วอาจส่งผลให้ Boiler ทำงานเพิ่มสูงขึ้นอย่างรวดเร็วทำให้เกิด Carryover สารเคมีในน้ำลอยออกมากับไอน้ำซึ่งอาจทำให้ผลิตภัณฑ์เสียหายได้
3.ค่าใช้จ่ายในการติดตั้งอาจสูงเกินเนื่องจากการเลือกขนาดวาล์วที่ใหญ่เกินไป
ระบบควบคุมที่ดีจะต้องประกอบไปด้วย
1. ไวต่อการเปลี่ยนแปลงของอุณหภูมิ ตัวอย่างถ้าถังขนาดใหญ่น้ำเย็นจะอยู่ที่ก้นภาชนะ
2. วาล์วควบคุมใหญ่พอที่จะทำงานในช่วงอุ่นเครื่อง และสามารถควบคุมการทำงานในช่วงทำงานได้อย่างแม่นยำ
3. ขนาดของวาล์วควบคุมจะต้องพิจารณาทั้ง warming up load และ running load เนื่องจากช่วงอุ่นเครื่องจะมีการใช้พลังงานมากดังนั้นถ้าเลือกวาล์วเพียงตัวเดียวให้ใช้ทั้งสองช่วง วาล์วจะมีขนาดใหญ่เกินไปสำหรับการทำงานในตอนหลังซึ่งเป็นสาเหตุของการควบคุมที่ไม่แน่นอนในตอนหลัง แนวทางสำหรับการเลือกวาล์วคือ
3.1 ในช่วงอุ่นเครื่องให้ติดวาล์ว manual by-pass เพื่อช่วยอุ่นเครื่องในตอนแรก
3.2 ติดตั้งวาล์วควบคุมสองอันขนานกันตัวที่หนึ่งสำหรับช่วงใช้งาน และ อีกตัวสำหรับช่วงอุ่นเครื่องโดยเมื่ออุณหภูมิได้ตามที่ต้องการวาล์วตัวนี้จะถูกปิด
โดยส่วนใหญ่ความผิดพลาดของการเลือกวาล์วก็คือการเลือกขนาดเท่ากับขนาดของคอยล์ ส่วนใหญ่ขนาดวาล์วจะเล็กกว่าขนาดท่อการเลือกควรดูจากคูมือในแต่ละยี่ห้อ ในส่วนของการต่อวาล์ว by-pass ควรเลือกท่อและวาล์วเท้ากับขนาดท่อหลัก
โดยทั่วไปเมื่อไอน้ำผ่านวาล์วควบคุมจะมีแรงดันสูญเสียที่วาล์ว โดยวาล์วทั่ว ๆ ไปขณะเปิดสุดแรงดันจะตกประมาณ 58% ซึ่งแรงดันที่ตกลงมีผลทำให้อุณหภูมิของไอน้ำที่เข้าสู่คอยล์ลดลงไปด้วย
วาล์ควบคุมแบบ เปิด/ปิด ด้วยไฟฟ้า
การทำงานของวาล์วประเภทนี้เมื่ออุณหภูมิของเหลวลดลงถึงจุดที่ตั่งค่าไว้ ระบบจะสั่งให้วาล์วเปิดอย่างรวดเร็วและเมืออุณหภูมิสูงกว่าที่กำหนดระบบจะสั่งให้วาล์วปิดอย่างรวดเร็วเช่นกัน ซึ่งอาการนี้อาจทำให้เกิด Water hammer ขึ้นในระบบได้ นอกจากนี้สำหรับการทำงานเมื่อวาล์วปิดลงแรงดันบางส่วนยังคงเหลืออยู่ในคอยล์ซึ่งยังสามารถแลกเปลี่ยนความร้อนได้อยู่ซึ่งอาจทำให้อุณหภูมิสูงขึ้นอีกได้ Temperature overshoots.
วาล์วควบคุมอุณหภูมิแบบอัตโนมัติ
ระบบวาล์วควบคุมประเภทมีข้อดีที่ทนทาน นอกจากนี้ยังไม่ต้องพึ่งพลังงานจากภายนอกในการทำงาน การทำงานจะเป็นระบบ on/off การควบคุมสามารถปรับอุณหภูมิได้ง่ายทำให้สามารถป้องกันการเกิด temperature overshoot ได้
ตำแหน่งการติดตั้งเซ็นเซอร์
ตำแหน่งการติดตั้งเซ็นเซอร์นับว่ามีความสำคัญเนื่องจากอุณหภูมิในถังใหญ่ ๆ จะไม่เท่ากันทั้งถังดังนั้นโดยปกติจะติดตั้งเซ็นเซอร์ที่ข้างถังตำแหน่งความสูงที่จะใช้งานหรือกึ่งกลางก็ได้ แต่ในกรณีที่ไม่สามารถเจาะถังได้อาจติดตั้งจากด้านบนในแนวตั้งก็ได้ แต่ต้องมั่นใจว่าขณะทำงานชิ้นงานจะไม่ไปกระแทกถูกถ้าชิ้นงานหรือของเหลวอาจก่อให้เกิดความเสียหายกับเซ็นเซอร์ ซึ่งอาจติดตั้ง Pockets เพื่อกันกระแทกเซ็นเซอร์ก็ได้แต่ต้องจำไว้ว่าถ้ามีการติด pockets การตอบสนองต่ออุณหภูมิของเหลวจะลดลงโดยเฉพาะถ้ามีช่องว่างของอากาศอยู่ภายใน pockets โดยส่วนใหญ่จะใช้น้ำกลั่นเติมในช่องว่างเพื่อเพิ่มความสามารถในการถ่ายเทความร้อนมาที่เซ็นเซอร์ ในกรณีที่ใส่เซ็นเซอร์จากด้านข้างไม่สามารถเติมน้ำได้อาจใช้จารบีแทนก็ได้